Breaking New Ground in Ex/ATEX Inspections – Part 1
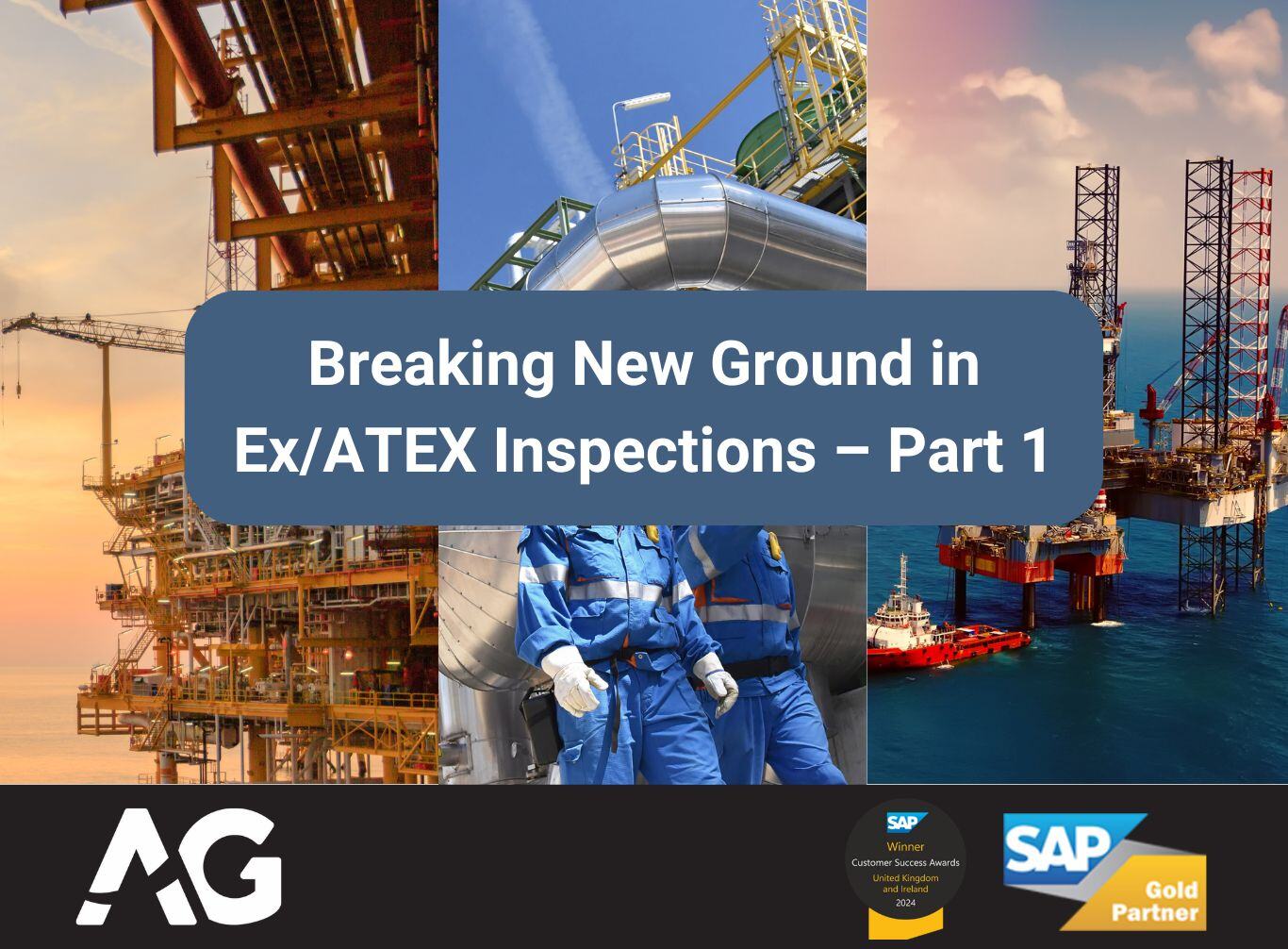
Introduction
In industries with potentially explosive environments—such as oil and gas, energy, and petrochemicals, maintaining stringent health and safety standards is not just regulatory; it's a critical safeguard against potentially catastrophic incidents. Ex/ATEX inspections play a pivotal role in this safety matrix, which is explicitly designed to prevent accidents by ensuring that all electrical equipment operates within strict safety parameters.
Historically, the failure to conduct thorough Ex/ATEX inspections has led to severe consequences. For instance, the 2005 Buncefield fire in the UK, one of the largest fires in peacetime Europe, was attributed to failures in safety checks and risk assessments, emphasising the disaster potential from overlooked safety protocols. Similarly, the 2010 Deepwater Horizon oil spill in the Gulf of Mexico, which resulted in massive environmental and economic damage, underscored the critical need for robust safety systems and regular inspections to manage operational risks effectively. Another poignant example is the Piper Alpha disaster in 1988 in the North Sea, where lapses in maintenance and safety checks led to the deadliest offshore oil platform catastrophe, claiming 167 lives.
These examples highlight the importance of routine inspections in general and Ex/ATEX, not only for compliance but also for protecting human lives and the environment. They also illustrate the necessity for industries operating in hazardous environments to adopt a reliable, efficient, and integrated approach to managing these safety checks. As we delve deeper into the operations and challenges of managing Ex/ATEX inspections, it becomes evident that enhancing the IT system to streamline and safeguard these processes is beneficial and essential for ongoing safety and operational success.
The Role of IT Solutions in Ex/ATEX Inspections
The effectiveness of Ex/ATEX inspections hinges on the seamless integration of three core elements:
- People: Skilled professionals who understand the complexities of hazardous environments.
- Processes: Standardised procedures that guide the execution of safety measures.
- Systems: Robust IT solutions that support people and processes in their roles.
IT solutions reinforce the connection between people, processes, and systems. They improve this relationship by:
- Facilitating Communication: Ensuring data and insights are seamlessly shared across teams.
- Automating Processes: Reducing reliance on manual input decreases the potential for human error.
- Providing Real-Time Data: Offering timely updates crucial for making informed decisions in dynamic and potentially hazardous environments.
Common Problems with IT Solutions Supporting Ex/ATEX Inspections
The more we speak to companies in the mentioned industries, the more we find that the IT solution in most companies struggles to keep up with the task. The most common problems are.
Data Fragmentation:
In asset-heavy industries, relying on multiple specialized IT systems for specific tasks is a common practice. This fragmented setup often leads to scattered data, making it difficult to build a comprehensive view that accurately reflects the business. ATEX inspections are no exception. While this fragmentation cannot be entirely avoided, it can be improved by reducing the number of systems through the adoption of IT solutions with broader capabilities.
Inadequate Real-Time Data:
IT systems that fail to provide real-time data hinder the ability to respond swiftly to potential hazards. Delayed data updates can result in missed opportunities to prevent incidents, compromising safety and operational efficiency.
Complex User Interfaces:
Ex/ATEX inspection processes involve various users, from maintenance office staff to field personnel. If IT solutions are not user-friendly and intuitive, these maintenance staff may abandon them. After all, their primary responsibility is to conduct inspections, not to struggle with complicated IT systems. This lack of usability can result in data gaps, rendering the systems partially ineffective.
Poor Integration with Existing Systems:
Ex/ATEX inspection software often operates separately from the leading Computerized Maintenance Management Systems (CMMS), and while these systems are theoretically capable of interfacing, they frequently fail in practice. This is due to various reasons, such as the complexity of the interfaces, which makes them difficult to support and maintain, and discrepancies in the level of detail handled by different systems. When new IT solutions do not seamlessly integrate with existing systems, they can create significant gaps in process flows and data continuity. Such integration challenges can lead to operational inefficiencies, escalated costs, and the risk of data inaccuracies.
Lack of Mobile Compatibility:
In today's mobile-first world, the absence of mobile compatibility in IT solutions limits access to systems in the field. For Ex/ATEX inspections, mobility is crucial for on-site technicians and engineers, severely hindering operational flexibility and real-time reporting.
Addressing Concerns and Paving the Way for Safer Operations for SAP Clients
The challenges mentioned above highlight the critical need for a robust, integrated IT solution to support Ex/ATEX inspections. In our next blog post, we'll introduce AG's Smart Ex solution, a comprehensive platform that tackles these concerns head-on for SAP Clients.
AG's Smart Ex addresses the limitations of traditional IT systems by offering:
- Single Source of Truth
Smart Ex sits within the SAP, consolidating work management, asset details, and Ex/ATEX inspection data into a single source. - Reduced IT Support Costs
By unifying all components within SAP, Smart Ex significantly lowers support costs. - Improved Visibility of Risks
Smart Ex's singular system of record and robust reporting capabilities provide deeper operational insights. - Improved Data Quality
The mobile functionality of Smart Ex allows field technicians to upload photos, notes, and voice recordings directly, enriching the data quality in SAP. - Improved Operational Efficiency
Up-to-date data empowers informed decision-making and allows for swift responses to potential risks and improved business efficiency.
By overcoming these common obstacles, AG's Smart Ex empowers companies to streamline Ex/ATEX inspections, enhance communication and collaboration, and ultimately significantly improve overall safety and operational efficiency.
Stay tuned for our next blog post, in which we'll explore the functionalities of AG's Smart Ex and how it can revolutionise your Ex/ATEX inspection processes!
Check out AG's Smart Inspections Ex/ATEX Video Series for more information!