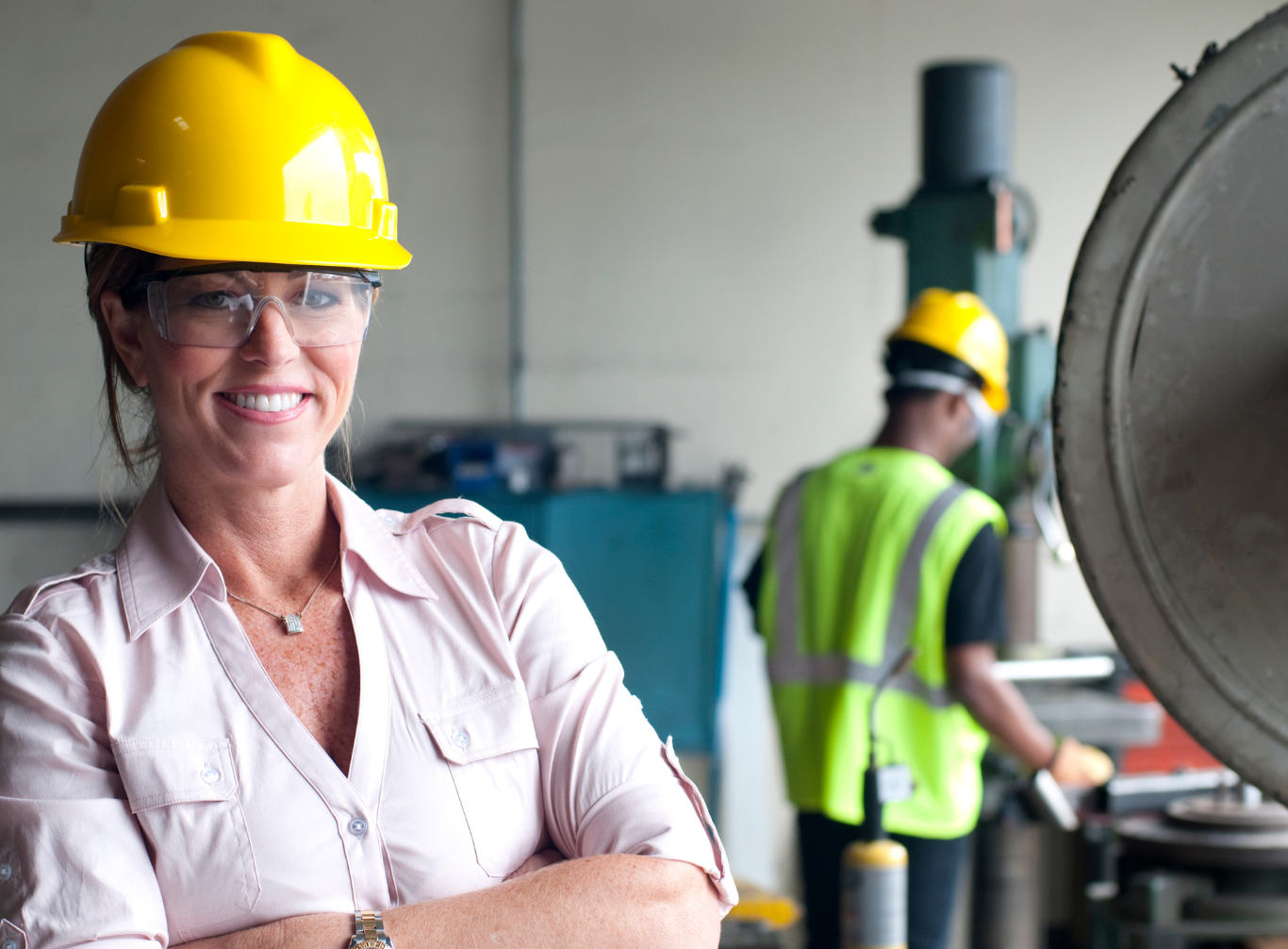
Shifting the focus to the future of manufacturing: Harnessing Industry 4.0 Solutions optimising the use of resources and reducing cost
A successful transition from the pilot stage to large-scale deployment of technologies of the Fourth Industrial Revolution continues to be elusive for many companies. Most of them need help to make this transition successful. For the manufacturing industry, unplanned downtime of productive assets remains a serious concern for management committed to delivering value to customers.
Burdening concerns for the manufacturing industry
CEOs insist on getting information on the cost of downtime to the hour, as they know extended periods of unplanned downtimes have severe implications for the company’s bottom line. Such concerns arise when organisation processes are not well aligned with the company's potential value and return on investment. On the other hand, the adoption of digital manufacturing continues to be uncertain due to the cost it incurs for implementing new solutions.
Need for innovation
Two significant factors that contributed to the Industry 3.0 revolution in the manufacturing industry were innovations in supply chain management and asset maintenance. Computer and Internet technologies were quickly adopted by industries to significantly change the way these functions were carried out – resulting in revolutionary improvements in productivity, quality, flexibility and sustainability.
Challenges of transitioning
Though contributions through innovations in the supply chain areas, such as Just-in-time supply process and e-commerce were prominent, changes in the asset management arena needed to be more visible and adequately acknowledged by industry leaders. In fact, while innovation in supply chain management reduced inventory cost to a great extent and made the overall process a lot smoother and transparent, it also meant that, for the maintenance manager, the likelihood of missing spare parts and consequently extended downtime went up.
Consequently, in recent times, it's understood that unless the asset management processes also keep up with technological advancements and innovations in other areas, the intended target of leveraging digital technologies to achieve significant gains in productivity will not be fully achieved. Asset managers need technologies that can reliably predict how critical assets will function in the foreseeable future - thereby allowing them to constantly revise and adapt their maintenance strategies to ensure overall value realisation for the organisation.
Adopting technologies to industrial scales
Although most asset managers have already moved beyond conventional preventive maintenance to predictive actions based on trend evaluations, such approaches are fast proving inadequate to the interconnected complex machinery that is now part of every modern industry.
Today’s asset management requires real-time data and a way to quickly convert them to meaningful information and produce analytic insights that could accurately predict potential future behaviour.
Some of the applications and technologies, collectively known as Industry 4.0, are designed to address such requirements from the industry. They allow for the real-time collection of critical data on a machine's performance and produce actionable, real-time information that helps asset management decisions.
SAP’s Intelligent Asset Management (IAM) suite for intelligent enterprises
A good example would be SAP’s Intelligent Asset Management (IAM) suite which consists of products such as Asset Strategy and Performance Management (ASPM), Predictive Asset Insight (PAI), Asset Intelligence Network, etc. These applications have taken Enterprise Asset Management (EAM) systems way beyond their conventional purposes of managing equipment maintenance and work management processes. ASPM, for instance, can help reliability engineers to identify an optimum balance between cost and risk of failures through a series of steps such as continuous evaluation of criticality, RCM/FMEA analysis and then using the results to fine-tune maintenance strategies.
SAP Predictive Asset Insights (PAI), another critical building block in the Intelligent Asset Management suite, can integrate data collected from the field using the latest technologies such as IoT and various other existing technologies, including sensors, and use artificial intelligence, machine learning and analytics to recognise patterns, apply data-science algorithms and project future incidents.
In short, Industry 4.0 solutions can be harnessed optimally based on each technology’s ability to address specific production and business problems, helping companies meet their commitment to customers and shareholders. So, EAM teams within manufacturing and service sectors must adopt these Industry 4.0 technologies to bring down unplanned downtimes to an absolute minimum.